The Craftsmen's Work of Hands
The Work of the Casting Men
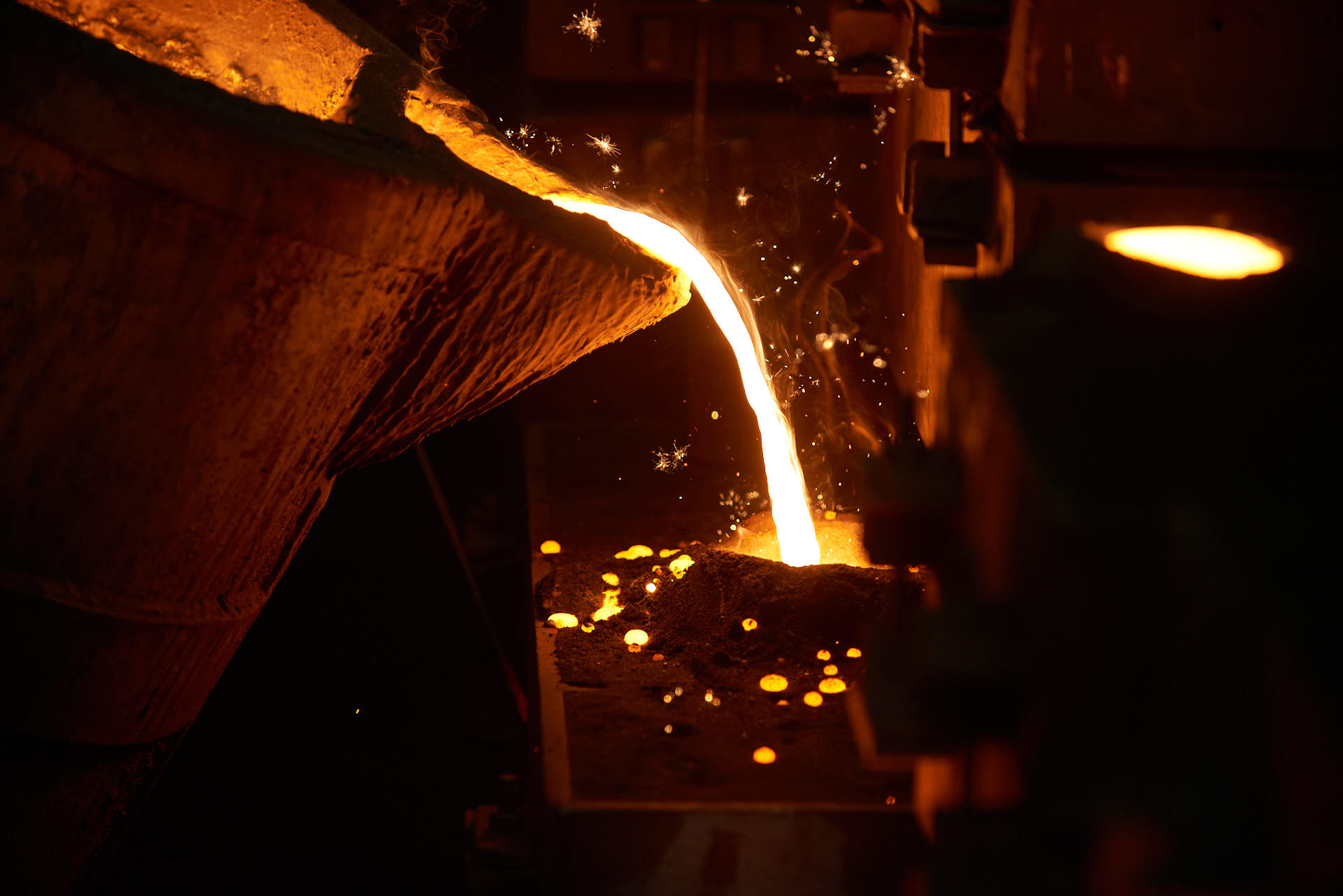
The Work of the Casting Men
The site evokes an image of a fledgling planet with thunderous roars, swirling sparks, and billowing dust in the shadowy atmosphere, disrupted by fleeting glimpses of struggling workers.
Casting is a fundamental process where molten metal is poured into a mold to shape an array of objects, ranging from a Buddhist statue and bell to modern industrial components like a car engine and electronics. Obviously, FUJI ROYAL’s roasters heavily rely on castings for parts exposed to high heat, such as a lid and a large dumper case. Cast iron stands out for its resilience to vibration, ability to create complex shapes, and ease of processing through machining.
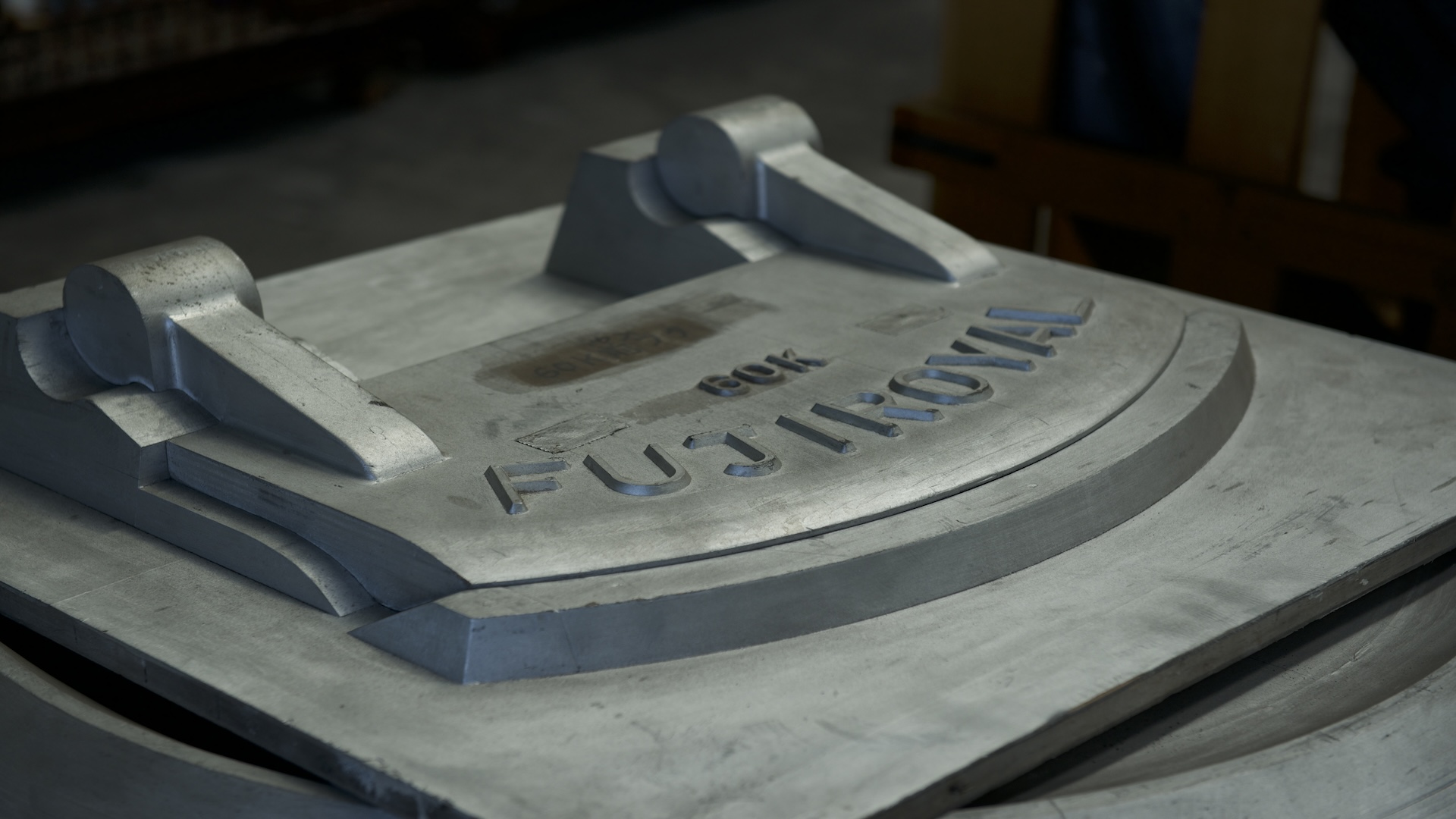
Unveil Mysteries of the Craft
Our esteemed partner, Kyoei Casting Co., Ltd., is one of the last 30 foundries in Osaka. Tadayoshi Tsujimoto, the company’s engineer, graciously takes us on a workshop tour.
The casting process begins with woodworkers creating a pattern, a wooden model based on a detailed product drawing. The pattern is buried in sand and then taken out once the mold hardens, leaving a hollow cavity of the desired shape. Molten iron is poured with great care into the mold, quickly solidifying. The figure is cooled, ejected, and finished by polishing.
“The key lies in pouring molten metal carefully but swiftly into a mold. Regardless of the object’s size, the process must be completed within a minute,“ notes Tsujimoto. Any delay risks premature solidification, as the metal cannot reach the mold’s edges and corners. On the other hand, rough handling can introduce impurities.
The process usually requires three workers—a crane operator, a ladle operator, and an assistant—with the crane operator’s role particularly critical, as Tsujimoto says:
The person holds their fate in his hand. Imagine the consequences if he spilled the boiling metal at 1350 °C! Despite its apparent simplicity, casting requires highly complicated brain work and expertise.
The Toughness
The workshop’s sand-blanketed floor serves as a safeguard against spills, but burns are inevitable amidst metal balls heated to over a thousand degrees.
A seasoned artisan chuckled, “Many modern regulations seem like a far cry from the realities of a foundry.” Safety boots, for example, make little sense to prevent molten metal burns. As depicted in the ancient pictures, casting workers in the past wore only loincloths and sandals so that they could flick off metal droplets from bare skin quicker than from cloth.
“Burns can penetrate deep into the skin, causing bad inflammation. Even medical advice helps little, except for scrubbing the wound off in a bath.”
We are left in stunned silence. Such profound dedication underpins our strength.
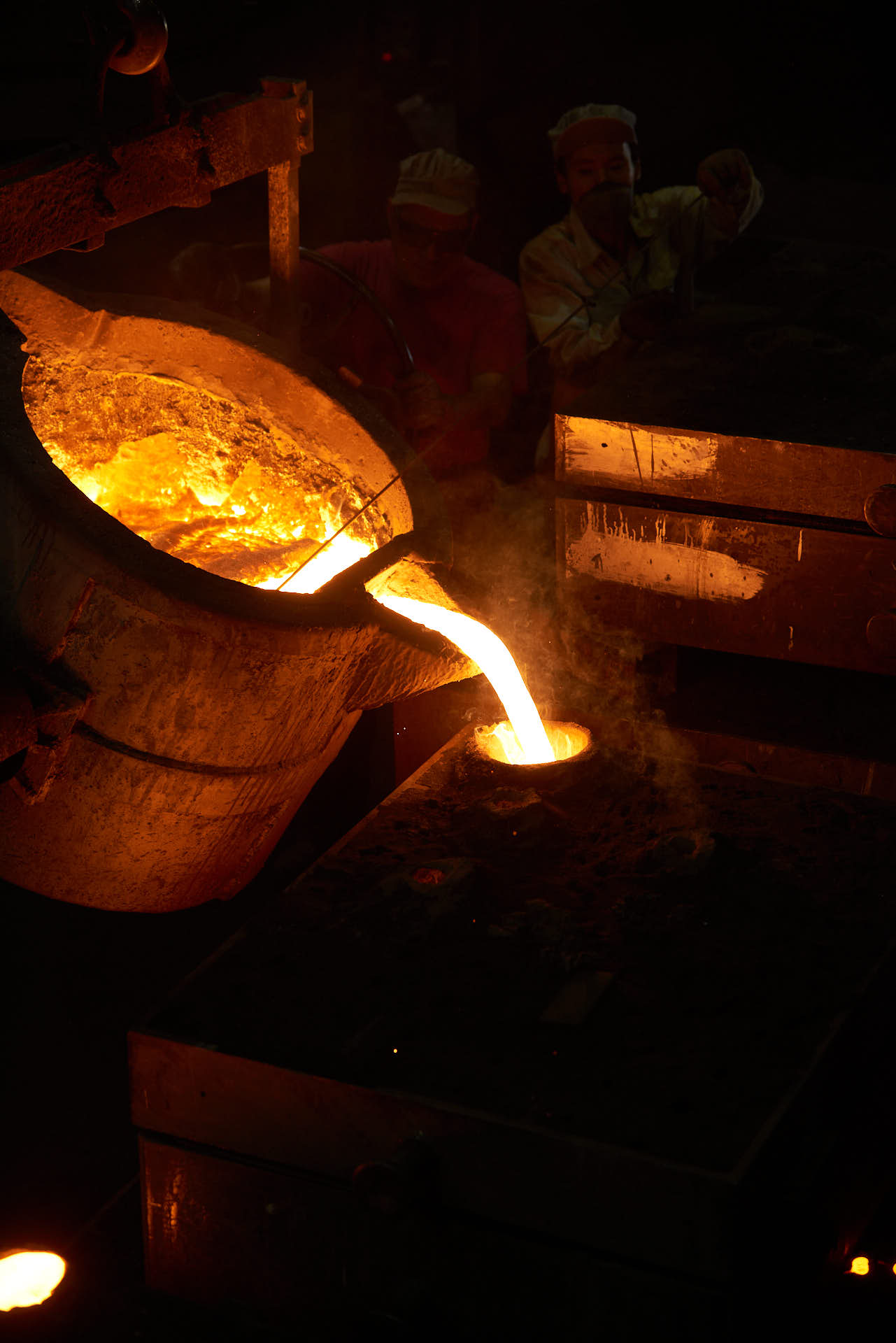