The Craftsmen's Work of Hands
Lathe Operator’s work
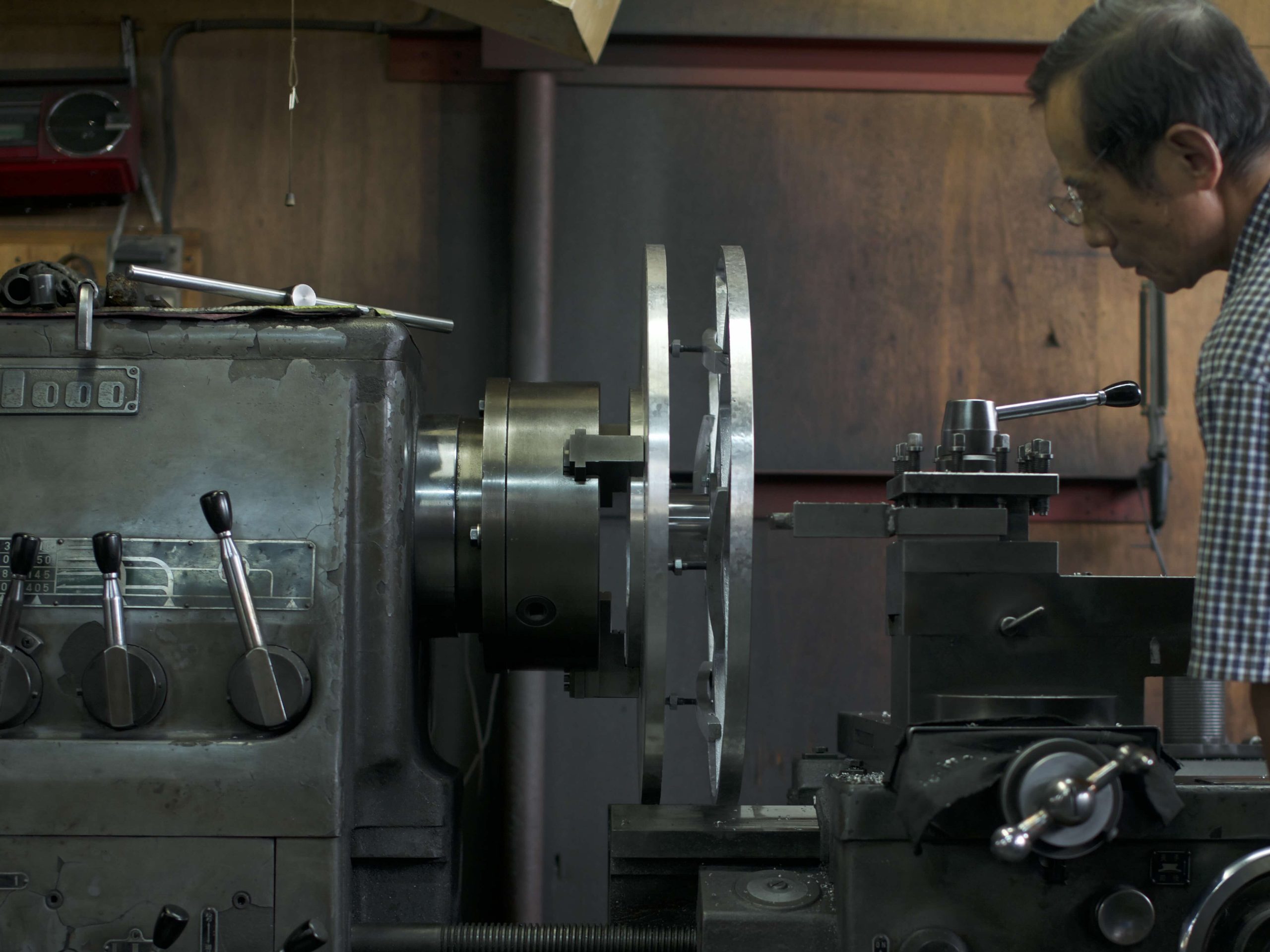
Lathe Operator’s work
The Star of Machining
A single-story factory is filled with a mixed scent of iron scrap and oil. Among briskly moving lathe workers, Tomosada Fujimoto smiles and recalls, “Back in the day, we didn’t have a roof here, and snow would fall inside. We’d light a fire to keep warm.”
The workshop Kiren Royal houses various kinds of equipment, from a radial arm drilling press and milling cutter to a vertical shaper. Those manual machines have been meticulously kept in good condition and used since the 1970s. Instead of giving a wordy explanation, Fujimoto grabs a handle and shows us how a lathe works. When the turning tool softly touches the surface of an iron block mounted on the rotating faceplate, it’s almost unbelievable to see a ribbon of hard metal peeling away from the spinning workpiece.
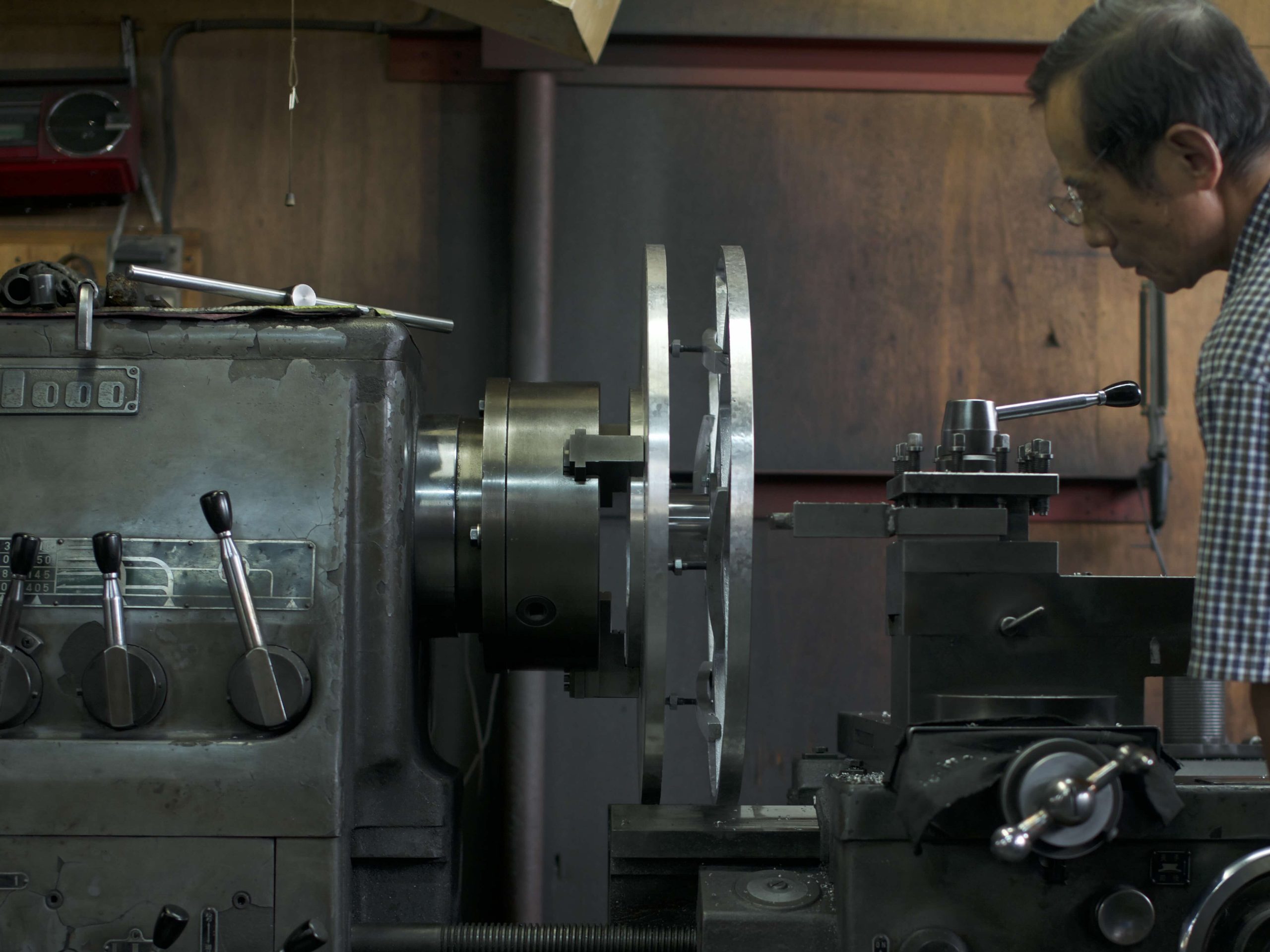
Before readymade and disposable cutters became prevalent in the 1960s, most machinists crafted their own turning tools. Like a blacksmith, they heated a piece of metal with bellows and a coke-fueled fire, beating it repeatedly with a heavy hammer. The shine of handmade, well-maintained tools symbolized their expertise and pride. Lathe work was, and hopefully is, considered the highlight of manufacturing.
Beyond Blueprints
Fujimoto’s first collaboration with Fuji Kouki was at the age of 20. His rugged hands have mastered the intricacies of milling different components ever since, such as a cast iron lid, damper lever, and more. Take a grid-shaped base for a cooling tray, for example: “Its top surface is shaved 0.3 mm more than its bottom because the top swells when a tray catches hot roasted beans. The thermal expansion of iron must be accounted for to ensure perfect function and proper assembly.”
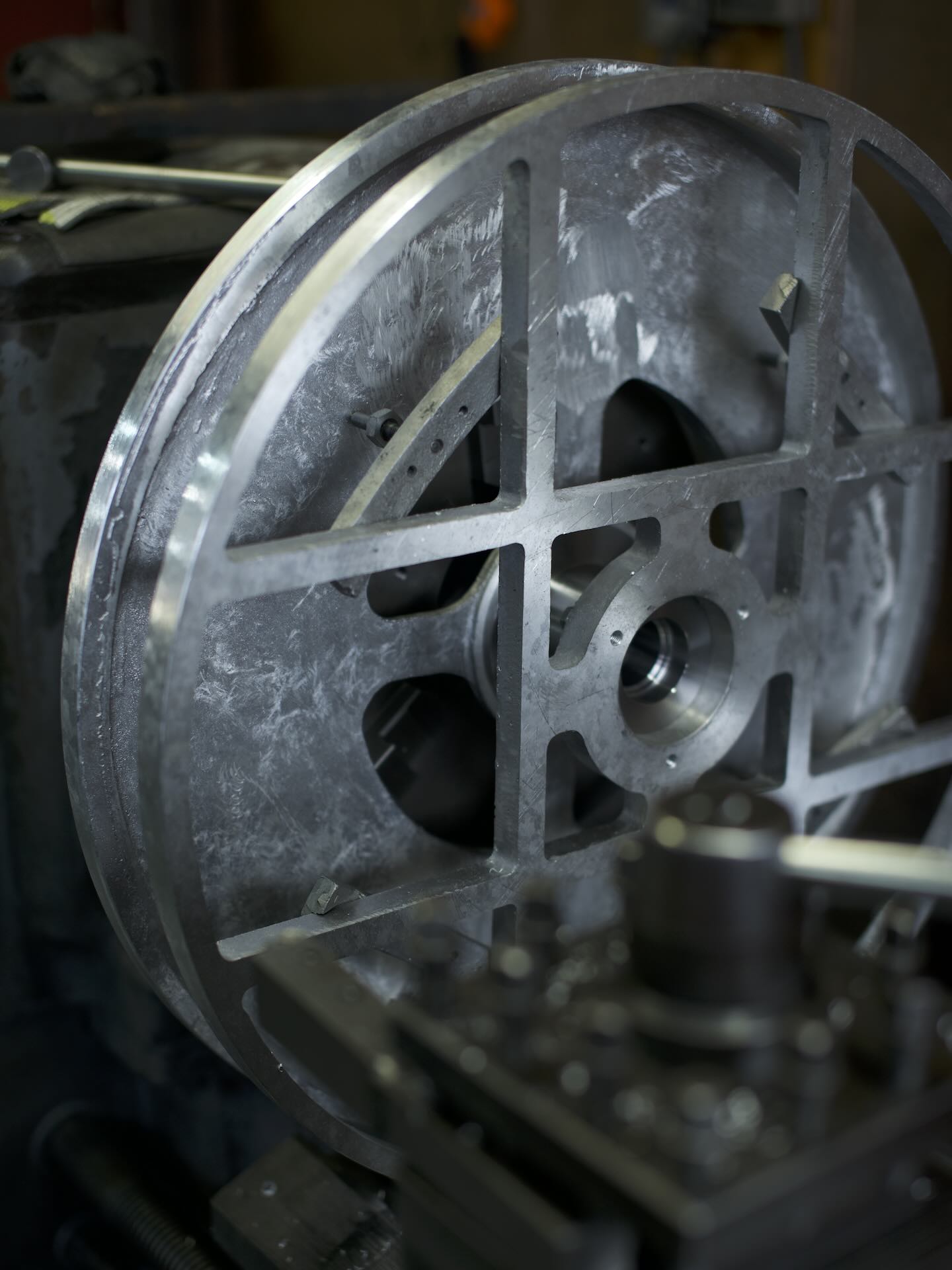
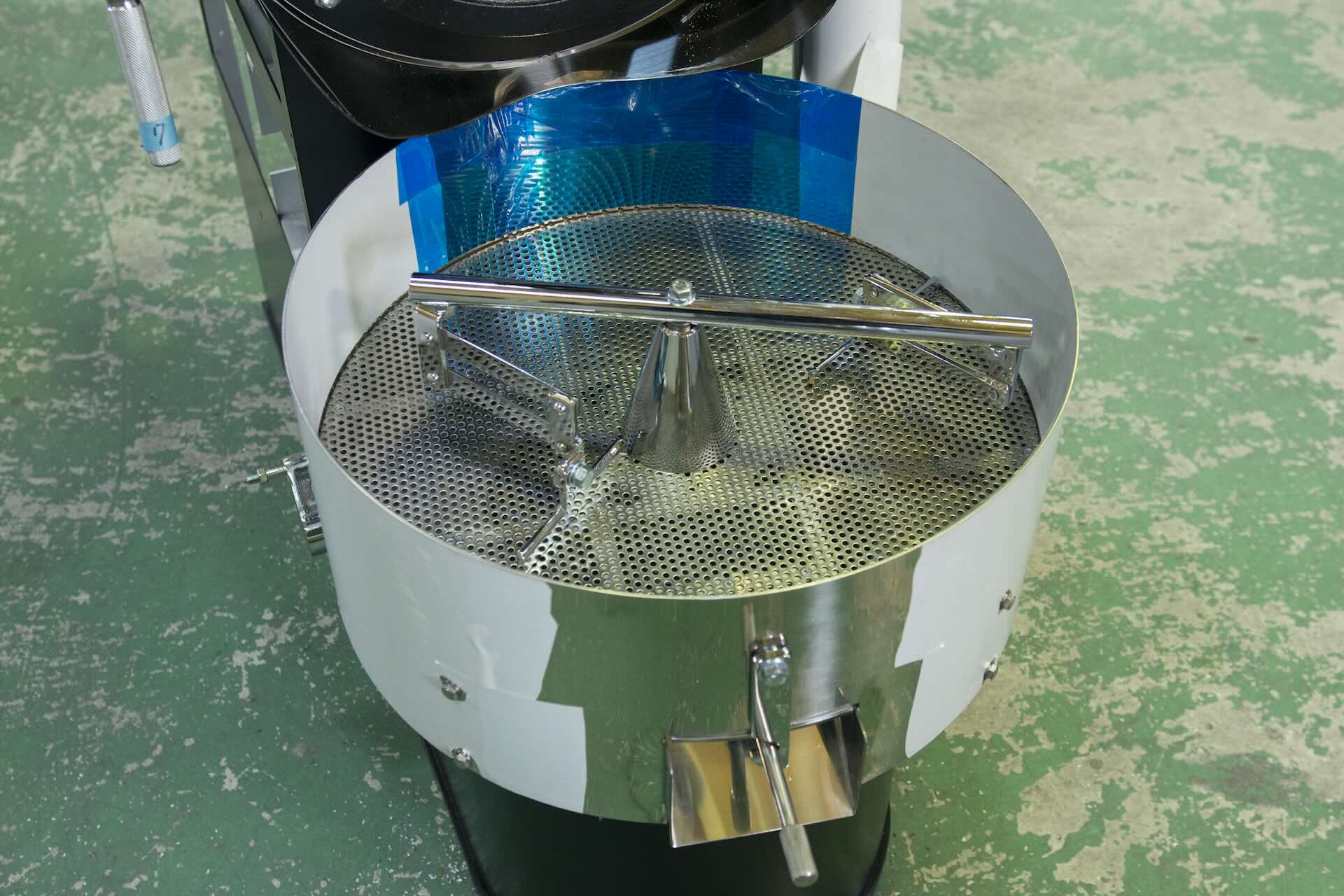
He adds, “Lathe workers often communicate with designers to have appropriate allowances.” Even if assembly is theoretically feasible, practical difficulties can arise when assembly workers manually tilt the milled components a little, adjust angles, and fit them together. Lathe expertise involves predicting subsequent manufacturing processes and considering factors not apparent in the blueprints.
Achieving the very measurements I aim for is the most rewarding. No matter how many years you dedicate to a component, it is still challenging and crucial to get its ideal measurement every time. It’s gratifying to hear that the assembly is going well.
So says Fujimoto, wiping sweat off and taking a break with a glass of juice. The physical and mental exertion to do the best signifies the core values of true craftsmanship.
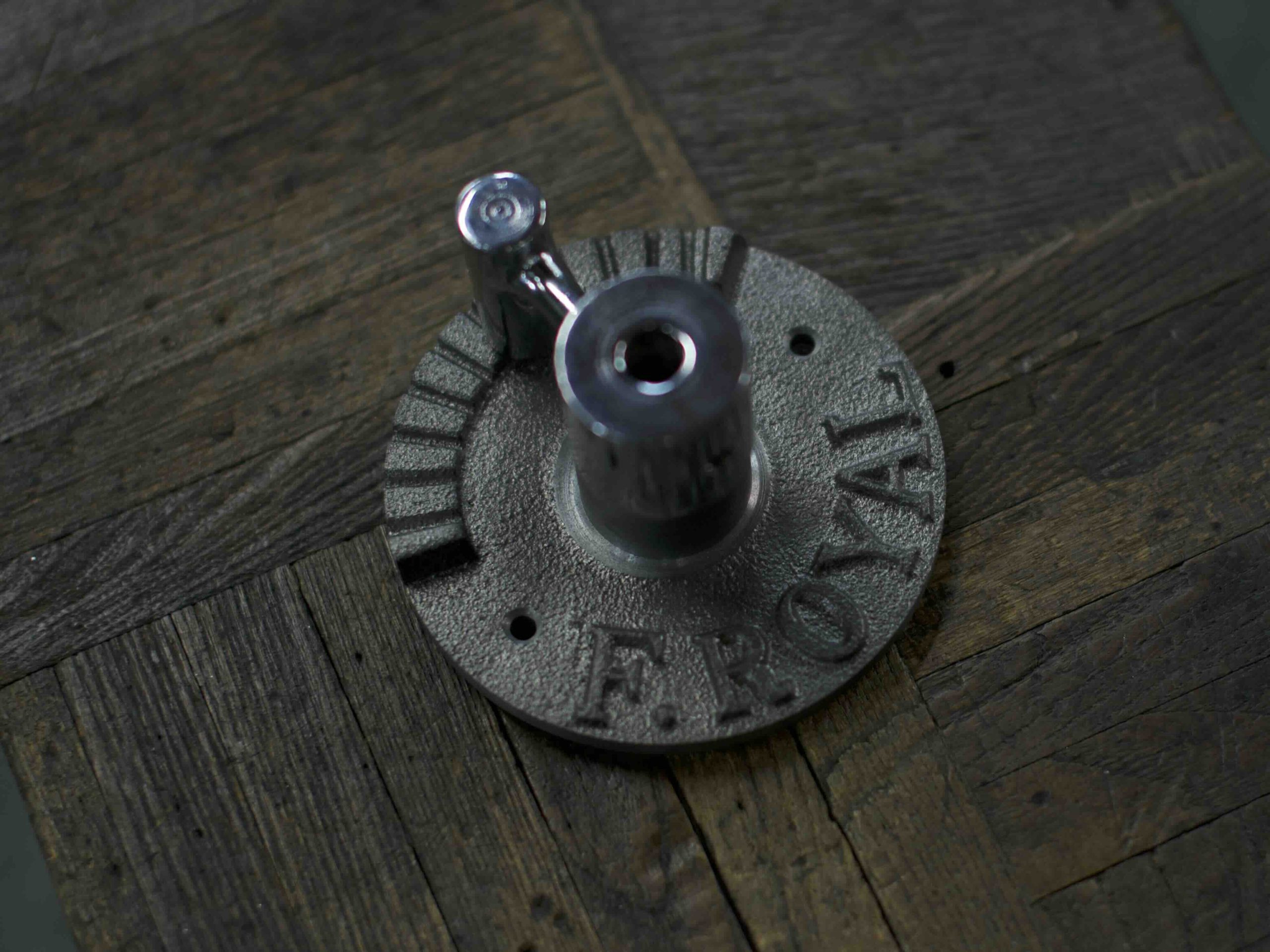